专业文库
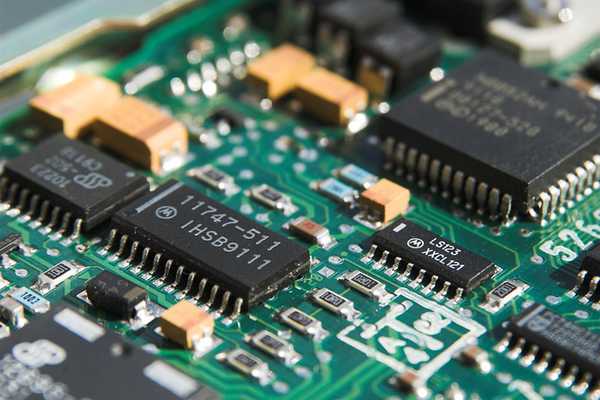
助焊剂和清洗工艺的选择在很大程度上决定了电子组件的制造良率和产品可靠性。我们将讨论清洁度要求,以了解PCB是否已清洗得足够洁净,足以满足其预期应用的功能要求。
行业清洁度标准
除了设定焊点的“接受或拒绝”标准等其他要求外,IPCA-610和J-STD-001还规定了电子组件的清洁度要求。以下是IPCA-610和J-STD-001最新版(H版)中关于清洁度要求的说明。请注意标准中使用了术语“应当(shall)”而不是“应该(should)”,以避免混淆。
行业通用清洁度要求
与许多其他质量验收要求一样,IPC规定由用户和供应商协商确定清洁度要求。下面将重点介绍IPC-A-610H和J-STD-001 H标准中的一些要点。
"除非设计或用户另有规定,残留物状况的可接受性应该在应用三防漆之前的制造过程中确定,如果没有应用三防漆,则在最终装配上确定。"
由于制造材料或工艺参数的变化更可能对最终产品残留物状况和产品可靠性产生影响,从而导致需要重新认证,因此清洁度要求取决于工艺控制参数。制造材料、工艺变更分为两类:重大变更或轻微变更,重大变更需要验证,轻微变更需要客观证据的支持。
认证测试通常更广泛。通常有证据支持的轻微变更较简单,包括持续时间较短的SIR测试或重点关注化学特性的测试。
同样,该标准规定由制造商和用户确定工艺变更的程度及相关要求的变更通知。但IPC提供了一些实用的指南:
1.不应该有可见的残留物,但免洗助焊剂残留物是可接受的。
2.阻碍电气测试或目视检测的助焊剂残留物不可接受。
3.同样,无光泽的外观可接受,有色残留物或生锈的外观不可接受。
4.任何可能导电的外来物不可接受,尤其当其违反最小电气间距要求时。
5.含有氯化物并导致腐蚀的白色残留物不可接受。
以下是标准中的更进一步指南:
除非用户另有规定,否则制造商应当认证影响助焊剂和其他残留物可接受水平的焊接、清洗工艺。客观证据应当可供审查。没有客观证据支持时,不应当使用萃取测试如ROSE、IC等测试方法认证生产工艺。
"支持的客观证据应是测试数据或其他文件——证明实际硬件的性能在使用环境的预期条件下没有受到不利影响。这可能包括:
1.表面绝缘阻抗测试(SIR),可能与离子色谱测试相结合,以证明残留物可接受水平。但是这里并没有说明具体的SIR值应该是多少。我将根据历史数据提供一些可能的SIR值,以此说明当遵循常见的工艺控制时,会期望得到的结果。
2. 历史记录——包括现场退货、保修服务记录和故障分析,证明交付的产品上的离子和其他残留物没有引起使用中的故障。
3.通电时,在模拟终端产品使用环境的极端温度和湿度条件下的电气测试结果。应该对电气故障进行故障分析,以确定是否由离子或其他残留物导致故障。可在产品认证或出厂验收测试期间进行该测试。工艺认证应当包括对返工工艺的认证。
“对于可见残留物,要求是经过清洗工艺的组件应当无可见残留物。然而实际上由制造商和用户协商确定对可见残留物的具体要求。”
IPC规定由用户和供应商根据其产品的应用来决定双方都可接受的要求。这些标准还提供了一些参考资料和白皮书,作为用户和供应商用于建立要求的附加指南。总之不同的用户和供应商对相同的应用及相同产品可能有不同的清洁度要求。我不确定这是否是好事。
对清洁度要求的看法
如上所述,IPC不会规定具体的清洁度要求。但它会指导如何建立要求。如前所述,IPC对视觉上可接受的残留物(如助焊剂、白色残留物和外来物等异物)有一些非常具体的要求。但是对于具体的清洁度要求(例如表面绝缘阻抗或溶剂萃取量(微克)),则需要根据实际情况自行确定。
许多人会争辩说,溶剂萃取测试仅与松香有关。这就是J-STD-001需要不断进行更新的原因。它的D版是2005年发布的。然而在15年后的今天,尽管我们使用的元件越来越多,且元件底部和PCB表面之间几乎没有间隙,但是最新的H版对清洁度的要求与D版却仍是相同的。那么从20世纪80年代开始,过去的几十年我们一直在做什么测试?你猜对了:溶剂萃取(又名 ROSE),该测试方法被应用于各种助焊剂和各类应用。
除了溶剂萃取外,另一种广泛使用的测试方法是表面绝缘阻抗测试(SIR)。以前行业使用的是侵蚀性水溶性助焊剂;根据抽样结果,在芯片组件下的生产板上,SIR值为500MΩ/每平方(每平方而不是每平方英寸)是可接受标准。我在英特尔公司工作时,该测试帮助我们发现了许多问题,例如,由于粘合剂中存在空洞,导致粘合剂固化曲线不良,从而截留助焊剂。此外还必须确保没有发运在现场可能具有腐蚀性的产品。
不对RE和OR助焊剂规定清洁度要求的理由是,当不知道这些助焊剂在未知的环境中会与哪些类型的基板、阻焊膜和涂层相互作用时,不可能使用可重复的测试方法制定验收要求。这个论点可能是正确的,但当涉及RO助焊剂时,我们也可以问相同的问题。此外,这个问题可以通过更保守的方式来解决,像我们对R0助焊剂所做的那样,在一个非常潮湿的环境中使用RE和OR助焊剂。如果使用RE和OR助焊剂并且可以承受的起在指南中的各种测试,那么我们可以在向火星发送载人任务时候应用,但是我们并不是都要把组件送到火星上去。如果遇到腐蚀问题,那么采用哪种助焊剂很重要吗?例如,如果您大量使用松香助焊剂进行返工,就可能会遇到腐蚀问题,并留下大量未被热激活而对PCB无腐蚀性的助焊剂。
清洁度要求建议
根据几十年来的历史经验,我认为需要考虑3个简单的要求(可能会受到行业标准如J-STD-001和IPC-A-610未来新版本的影响)。
1.除了免清洗助焊剂残留物外,应该无可见助焊剂残留物。无论PCB上有何种助焊剂残留物,都不应出现白色或腐蚀性的外观。
2.由于溶剂萃取(ROSE)是常用的测试方法,因此行业常用的10.06 µg/in2数值应用于所有助焊剂。但是如果用户和供应商同意,也可以使用其他测试方法,如离子色谱(IC)或双方均可接受的其他测试,一些公司用于IC测试的NaCl等效水平为2.5µg/in至4.5µg/in。
3.最重要的要求是,至少要在使用前对助焊剂进行鉴定,在100VDC的湿度室中测量的表面绝缘阻抗值应该为500MΩ/平方,以检测在几乎没有托高的元件下方的助焊剂残留物。
考虑到低托高元件的广泛使用,如BTC、LGA和细间距QFP(元件底部和PCB表面之间几乎没有间隙),在这三种测试中,SIR测试是最可靠的测试。如果元件下方截留有任何助焊剂残留物,SIR值将不会满足500MΩ(10的8次方)的要求。大多数PCB在适当清洗后,无论使用何种助焊剂,其清洁度都会高达10的12次方或更高。PCB应该有两个SIR梳形电路(用于关键应用产品的生产板)。其中一个梳形电路包含具有最低托高的元件,而另一个梳形电路则没有元件。由于该位置没有助焊剂,SIR值会很高。因此可以将其视为一个基准条件。具体详情,可参考第1项参考资料中介绍的SIR梳形电路指南。
最后,需要注意的是,没有最好的助焊剂、最好的清洗方法或确定清洁度的最佳方法。这些变量取决于具体的应用。因此使用本专栏讨论的指南,用户必须根据特定应用的经验数据建立对助焊剂、清洗和清洁度测试的要求。这意味着应该在随机选择的组件上进行清洁度测试(SIR、溶剂萃取及目检)。良好的工艺控制是无可替代的,因为如果一块不合格的PCB通过了清洁度测试,那么错误的组装批次将无法被召回、无法重新清洗或无法重新测试。
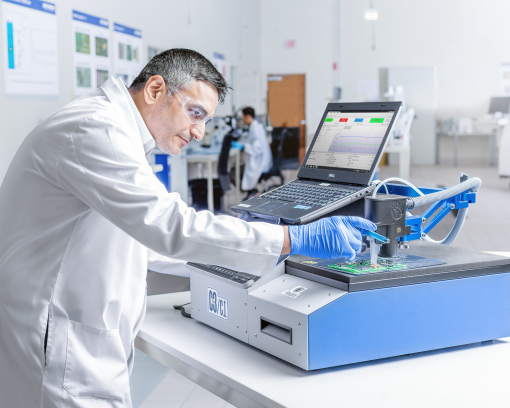
在元器件封装或组装工艺中,虽然有些污染物仅仅影响产品外观,但离子型污染物在潮湿或存在电位差的条件下,会导致电化学腐蚀及漏电失效,在高温、高湿和偏置电压共同作用下会出现电化学迁移等失效。因此,管控离子型污染物已经成为高可靠性产品生产制造中的必要环节。
当前常见的离子污染物测定方法主要有以下三种。ROSE测试法(溶剂萃取电导率法)曾是业界多年惯用的离子检测手段,但因其仅能以氯化钠当量表示所有离子污染总量而无法解释离子污染物的组成,根据IPCJ-STD-001 最新版标准及IPC-WP-019,该方法如今已不能作为产品及工艺认证的接收标准,更适合于制程监控;IC离子色谱法一般参考IPC-TM-650 2.3.28或2.3.28.2标准,能精确测试阴阳离子和弱有机酸的种类和含量。具体操作方法是将待测元器件或PCB板放进高清洁度的专用密封袋中,加入一定体积的萃取液,萃取液一般为75%异丙醇和25%去离子水(体积比)或10%异丙醇和90%去离子水(体积比),80℃水浴1小时,将一定体积的萃取液注入到离子色谱仪中进行定性和定量分析;而C3局部污染测试法的原理是使用去离子水蒸汽从局部(0.1in²)测试点上将萃取样品提取出,并基于规定的漏电流指标给出“clean”或“dirty”的判定,从而判定该区域是否干净。IC和C3两种方法分别侧重对离子的定性定量和局部区域快速定性,适合满足客户的不同测试需求。
图 | ROSE测试、IC和C3的优缺点对比
根据ZESTRON R&S多年的分析经验,采用常规整板提取方法制样进行的离子色谱分析有时并不能检测出任何异常偏高的离子污染物,其测试结果可能无法帮助准确地找到失效的根源,甚至可能导向错误的解决路径。相比之下,在特定情况如进行失效分析或者风险评价时,ZESTRON R&S推荐选择“C3+IC”的检测组合拳。通过充分发挥C3和IC的独特优势,先后对潜在发生失效的区域进行快速污染判定及对污染物中离子完成定性定量,从而精准评价产品风险或者锁定失效原因。在ZESTRON北亚区分析实验室,ZESTRON已经为多家汽车电子及半导体行业头部企业提供IC和C3组合使用的离子清洁度测试服务,帮助客户开展失效分析,检测焊接之后的表面清洁度是否达标,以及判定表面是否具备涂覆或绑定的条件。凭借ZESTRON全球的智力资源和先进的北亚区分析中心,ZESTRON R&S能够对IC、BGA等元器件产品、PCB、PCBA等电子半成品及成品进行全面而精准的表征和评价,同时结合专业经验为客户提供详细的分析报告并推荐纠正措施。
ZESTRON R&S采用的技术手段包括但不限于:高清数码显微镜目检、离子色谱法(IC)、离子污染度测试(ROSE)、傅里叶变换红外光谱法(FTIR)、涂覆可靠性测试(CoRe Test)、颗粒物测定/技术清洁度(Technical Cleanliness)、扫描电子显微镜/X射线能谱分析仪(SEM/EDX)、X射线光电子能谱(XPS)、俄歇电子能谱(AES)、涂覆层测试(Coating Layer Test)、助焊剂测试/树脂测试(Flux/Resin Test)、接触角测量(Contact Angle)、表面绝缘电阻测量(SIR)、差热分析(DTA)等。如您需要分析、评估和咨询服务、或更加灵活系统的培训方式,ZESTRON R&S可以基于您的具体需求提供定制化的服务方案。欢迎发送邮件至